Quick Guide:
- Purpose: Keep machinery running efficiently and safely
- Benefits: Reduces downtime, saves money on repairs, extends equipment life
- How: Regular inspections, timely maintenance, and keeping good records
Preventive maintenance is essential, especially if you hate surprises like unplanned machine stoppages that can cost you time and money. It's about being proactive rather than reactive. Think of it as ensuring your manufacturing outfit is always in top form, ready to tackle the day without hiccups. A well-drafted schedule helps you stay ahead, ensuring that potential problems are dealt with before they evolve into significant issues. It's not just about saving on costs; it's about providing safety, productivity, and reliability.
By using templates, you can streamline the creation of your preventive maintenance schedule. Templates provide a structured approach, ensuring you cover all necessary aspects efficiently. They can be easily customized to fit your unique needs, making the process faster and easier.
Infographic Summary:
- Identify all assets: List every piece of equipment and machinery.
- Set maintenance tasks and intervals: Determine what needs to be done and how often based on manufacturer guidelines and usage patterns.
- Use a CMMS: Implement preventative maintenance software to organize, schedule, and track maintenance tasks.
- Monitor and adjust: Continuously review and refine your schedule to keep it practical.
This roadmap makes the journey to a hassle-free, effective maintenance strategy straightforward and manageable.
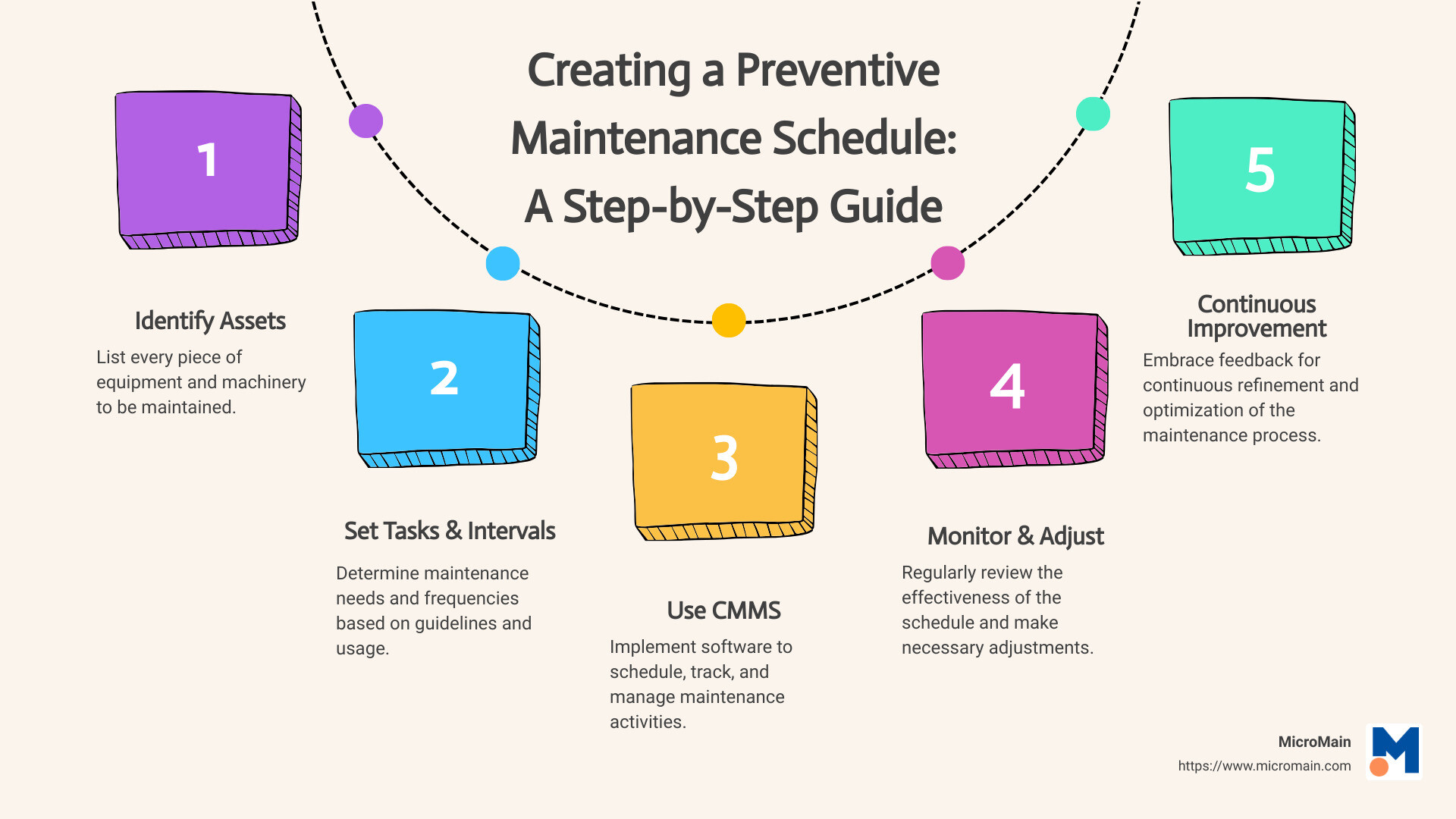
Understanding Preventive Maintenance
Preventive maintenance is your go-to strategy when it comes to keeping your operations smooth and reducing unexpected breakdowns. But before creating a robust preventive maintenance schedule, distinguish between predictive and preventive maintenance and understand the goals and cost-effectiveness of preventive maintenance.
Predictive vs Preventive
While preventive and predictive maintenance aim to avoid equipment failure, their approaches differ. Preventive maintenance is scheduled regularly, regardless of the equipment's current condition. It's like visiting the dentist every six months for a check-up, even if your teeth seem fine.
On the other hand, predictive maintenance relies on the actual condition of the equipment to schedule maintenance. This method uses sensor data and other indicators to predict when maintenance should occur. Imagine a smartwatch that alerts you to see a doctor based on your heart rate trends.
Both methods have their place in a comprehensive maintenance strategy, but preventive maintenance is more accessible for most organizations and provides a solid foundation for equipment care.
The primary goal of preventive maintenance is straightforward: to avoid the inconvenience and costs of equipment breakdowns. This proactive approach aims to:
- Extend the lifespan of assets by keeping them in optimal condition.
- Reduce downtime by scheduling maintenance that does not interrupt operations.
- Lower costs by avoiding expensive emergency repairs and inefficient operation due to worn equipment.
- Improve safety by preventing accidents caused by failing equipment.
Cost-effectiveness
Investing in preventive maintenance saves money in the long run. While it might seem like an added expense, the cost of preventive maintenance is often significantly lower than the cost of emergency repairs and the downtime those emergencies create. According to a source from MicroMain, a well-structured preventive maintenance program can reduce operational costs by as much as 12-18%.
Moreover, preventive maintenance can also lead to utility bills and spare parts savings. By keeping equipment running efficiently, you use less energy and reduce the wear and tear that leads to part replacements.
In summary, understanding the difference between predictive and preventive maintenance, along with recognizing the goals and the cost-effectiveness of preventive maintenance, is crucial for any organization looking to improve its maintenance operations. Companies can enjoy smoother operations, extended equipment lifespans, and significant cost savings by focusing on preventive measures.
With this foundational knowledge, we're ready to delve into the steps for Creating a Robust Preventive Maintenance Schedule using templates and best practices.
Key Components of a Preventive Maintenance Schedule
Understanding its key components is essential when creating a robust preventive maintenance schedule. This involves identifying the assets, equipment, vehicles, inspections, and tasks that will form the backbone of your maintenance program. Let's break down these components to ensure your schedule is comprehensive and practical.
Assets, Equipment, and Vehicles
The first step in crafting your maintenance schedule is taking inventory of your assets. This includes everything from heavy machinery and vehicles to smaller pieces crucial for daily operations. The goal is to maintain each asset properly to avoid unexpected breakdowns and extend its lifespan.
- Critical Assets: Focus on essential assets to your organization's success. These are usually high-cost items with a high likelihood of failure if improperly maintained.
- High Costs & Failure Likelihood: Consider the financial impact and safety risks associated with each asset's failure. This helps prioritize maintenance tasks based on cost-effectiveness and risk mitigation.
Selecting the Right Maintenance Triggers
Determining when maintenance should occur is crucial for creating an efficient schedule. There are three main types of maintenance triggers:
- Time-based: Maintenance tasks are performed regularly, monthly, or annually, regardless of the asset's condition.
- Usage-based: Maintenance is triggered by how much an asset is used, for example, every 1,000 hours of operation or every 10,000 miles driven.
- Condition-based: Maintenance tasks are performed based on the actual condition of the asset, determined through inspections and monitoring.
Each trigger type has its benefits and is suitable for different assets. Choosing the right trigger ensures that maintenance is performed when needed without wasting resources on unnecessary tasks.
Utilizing Preventive Maintenance Software
Implementing a Computerized Maintenance Management System (CMMS) can significantly streamline the creation and execution of your preventive maintenance schedule. A CMMS can automate scheduling, track maintenance history, and help manage work orders efficiently. This technology is a game-changer for maintenance teams, allowing for more accurate planning and execution of maintenance tasks.
To better understand how CMMS can transform your maintenance operations, look at how MicroMain's CMMS simplifies maintenance scheduling and management.
Creating a robust preventive maintenance schedule is about more than just listing tasks and setting reminders. It involves a strategic approach to understanding your assets, determining their maintenance needs, and using the right tools to ensure tasks are performed efficiently and effectively.
By focusing on these critical components, you can develop a preventive maintenance schedule that minimizes downtime, extends asset lifespans, and saves costs in the long run.
Leveraging templates for efficiency will be our next focus, ensuring that your preventive maintenance program is robust and streamlined for maximum effectiveness.
Steps to Create a Robust Preventive Maintenance Schedule Using Templates
Creating a robust preventive maintenance schedule doesn't have to be a daunting task. Using templates and a structured approach, you can streamline the process and ensure your equipment remains in top condition, reducing downtime and saving costs. Here's how:
Step 1: Asset Inventory
First off, list all your critical assets. This includes machinery, vehicles, and equipment vital to your operations. Consider aspects like high costs of failure and the likelihood of breakdowns. This step sets the foundation for your maintenance schedule.
Step 2: Determine Maintenance Priorities
Not all assets are created equal. Conduct a criticality analysis to understand which assets significantly impact production, safety, and regulatory compliance. This helps you allocate your maintenance efforts where they're needed most.
Step 3: Selecting the Right Maintenance Triggers
Deciding when maintenance should occur is crucial. You can choose from:
- Time-based: Maintenance occurs after a set period.
- Usage-based: Triggered by usage metrics, like hours of operation.
- Condition-based: Initiated when specific conditions are met, indicating potential failure.
Each trigger type has its place, and your choice should align with the nature of each asset and its operational context.
Step 4: Utilizing Preventive Maintenance Software
A Computerized Maintenance Management System (CMMS) is invaluable here. It automates work orders, centralizes asset information, and provides advanced reporting features. A CMMS can take the guesswork out of maintenance scheduling, making it easier to manage and track.
Step 5: Implement and Train
Roll out your preventive maintenance schedule, starting with a pilot program. Ensure your team is well-trained in their roles and how to use any new software. Engaging your team early on ensures smoother implementation and better adherence to the maintenance schedule.
Step 6: Monitor, Measure, and Adjust
Finally, use Key Performance Indicators (KPIs) to track your maintenance program's success. Continuous improvement should be your goal. Regularly review your schedule and make adjustments based on performance data and feedback from your team. This ensures your preventive maintenance schedule remains effective and aligned with your operational needs.
By following these steps and leveraging the efficiency of templates, you're well on your way to creating a robust preventive maintenance schedule that keeps your operations running smoothly and efficiently. A well-planned schedule is critical to minimizing disruptions, extending the life of your assets, and optimizing your maintenance efforts.
Leveraging Templates for Efficiency
Efficiency is critical when it comes to creating a robust preventive maintenance schedule. Templates can be a game-changer. Let's dive into why templates are beneficial, how they can be customized for your needs, and provide real-life examples.
Template Benefits
Templates for preventive maintenance schedules offer a range of benefits:
- Speed: Jumpstart the scheduling process. Instead of starting from scratch, templates provide a structured format that you can quickly fill in with your specific details.
- Consistency: Ensure that all necessary information is captured every time. This uniformity makes it easier for everyone to read and understand the schedule.
- Accuracy: Templates can help reduce errors by providing predefined fields that prompt you to enter all the required information.
- Customization: Most templates are designed to be adjusted. You can tweak them to suit your specific maintenance needs and priorities.
Customization
One size does not fit all in preventive maintenance. Your facility might have unique equipment, different operational pressures, or specific regulatory requirements. Here's how you can customize templates:
- Identify Critical Assets: Start by listing assets that are crucial for your operations. This ensures they are prioritized in your schedule.
- Adjust Maintenance Frequencies: Depending on the asset's usage rate and criticality, adjust how often maintenance tasks need to be performed.
- Incorporate Industry Standards: Ensure your template reflects specific industry guidelines or standards for equipment maintenance.
Examples
Let's look at practical examples where templates have streamlined the preventive maintenance process:
- Vehicle Fleet Management: A transportation company used a template to schedule regular checks for their fleet. They could efficiently plan for oil changes, tire rotations, and brake inspections by customizing the template to include mileage-based triggers.
- Manufacturing Equipment: A manufacturing plant implemented a template to manage the maintenance of their machinery. The template allowed them to input specific inspection points for each machine type, ensuring critical components were regularly evaluated for wear and tear.
- Facility Maintenance: A large office complex utilized a preventive maintenance template for its HVAC systems, elevators, and safety equipment. The template helped them schedule monthly, quarterly, and annual checks, ensuring tenants a comfortable and safe environment.
For those looking to get started or improve their preventive maintenance program, leveraging a maintenance software solution can significantly enhance the effectiveness of your templates. Software solutions can automate scheduling, remind you of upcoming tasks, and even adjust maintenance intervals based on real-time data.
By understanding the benefits, customizing to fit your needs, and learning from real-world examples, you can leverage templates to enhance the efficiency of your preventive maintenance schedule significantly. This approach saves time and ensures that your maintenance tasks are performed consistently and accurately, leading to better asset management and longer equipment lifespans.
Frequently Asked Questions about Preventive Maintenance Schedules
When creating a robust preventive maintenance schedule, several questions frequently emerge. Addressing these can help clarify the process and ensure your schedule is effective and efficient.
What is the difference between preventive and predictive maintenance?
Preventive maintenance is about regular, scheduled maintenance to prevent failures before they happen. It's based on time or usage intervals—like oil changes every 3,000 miles. On the other hand, predictive maintenance uses data and condition-monitoring tools to predict equipment failures before they occur. This approach relies on vibration analysis, thermal imaging, and other diagnostic techniques. While preventive maintenance is scheduled regardless of equipment condition, predictive maintenance is performed when specific indicators show signs of decreasing performance or upcoming failure.
How often should preventive maintenance be performed?
The frequency of preventive maintenance varies widely depending on the asset, its use, and the environment in which it operates. Generally, manufacturers provide recommendations for maintenance intervals in equipment manuals. However, these guidelines should be adjusted based on actual usage and conditions. For example, a vehicle in a high-dust environment might require more frequent air filter changes. Utilizing a CMMS can help manage and adjust those schedules based on real-world data, ensuring maintenance is performed precisely when needed, early enough, or too late.
Can preventive maintenance schedules be adjusted over time?
Absolutely. They should be. A preventive maintenance schedule isn't a set-it-and-forget-it tool. It requires ongoing adjustments based on several factors, including changes in equipment usage, updates to manufacturer recommendations, and insights gained from maintenance history. Regularly reviewing and updating the schedule helps improve its effectiveness, reduce costs, and extend the lifespan of your assets. This continuous improvement cycle ensures that your preventive maintenance program evolves with your operational needs and technological advancements.
In summary, creating a robust preventive maintenance schedule involves setting up tasks and understanding the nuanced differences between maintenance types, determining the right frequency for your specific context, and adjusting the plan as new information becomes available. This approach ensures that your preventive maintenance efforts are as effective and efficient as possible, leading to improved asset reliability and cost savings.
Conclusion
Creating a robust preventive maintenance schedule is more than just a task; it's a strategic approach that ensures long-term benefits, safety, and cost savings for your organization. By following the steps outlined, using templates for efficiency, and leveraging the power of CMMS software, organizations can transform their maintenance operations from reactive firefighting to proactive guardianship of their assets.
Long-term Benefits
A well-implemented preventive maintenance schedule extends the life of equipment, reduces downtime, and ensures that operations run smoothly and efficiently. This saves money in the short term by avoiding costly emergency repairs and adds value to your assets over time. The consistency provided by a preventive maintenance plan results in reliable asset performance, which is critical to achieving operational excellence and staying competitive.
Safety
One of the most critical aspects of preventive maintenance is the enhancement of safety within the workplace. Regular maintenance checks and repairs prevent accidents and ensure a safer environment for employees and customers. By proactively identifying and addressing potential hazards before they lead to incidents, organizations underscore their commitment to safety and compliance with regulatory standards.
Cost Savings
While seemingly substantial, the initial investment in setting up a preventive maintenance schedule pales compared to the cost savings realized in the long run. Reduced unplanned downtime, fewer emergency repairs, and extended asset life spans collectively contribute to significant financial savings. Moreover, the data-driven insights provided by preventive maintenance software enable organizations to make informed decisions about asset management, further optimizing maintenance expenditures.
In conclusion, the journey from paper to digital in facility management, mainly through the adoption of CMMS software, revolutionizes how organizations approach maintenance. Creating a robust preventive maintenance schedule is not just about preventing equipment failure; it's about embracing a culture of continuous improvement, safety, and efficiency. As we've seen, the benefits extend far beyond immediate operational gains, contributing to your organization's sustainable, productive future.
Let this be a call to action: embrace preventive maintenance as a strategy and a cornerstone of your organization's operational philosophy. The road ahead may require effort and adaptation, but the destination—a safer, more efficient, cost-effective operation—is well worth the journey. Discover how our industry-leading CMMS software can be integral to that journey, providing you with the tools you need to succeed.